The Importance and Functionality of the Desilter in Drilling Rigs
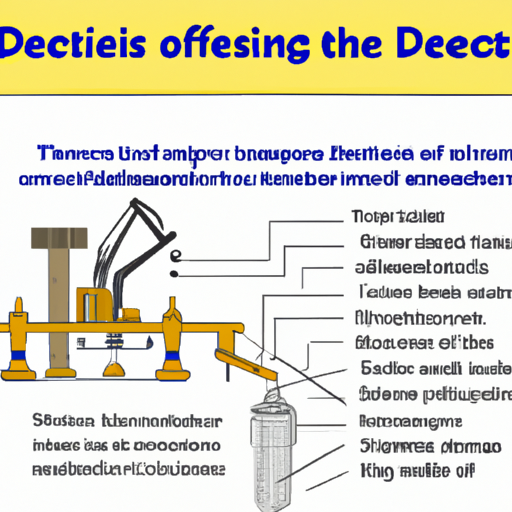
Introduction (word count: 150)
Drilling rigs are crucial in the extraction of valuable resources from the Earth's subsurface. These rigs employ various equipment and technologies to ensure efficient and safe drilling operations. One such critical component is the desilter, which plays a pivotal role in maintaining drilling fluid cleanliness and overall performance. In this article, we will explore the significance of desilters in drilling rigs, their functionalities, and their impact on drilling operations.
1. Understanding the Desilter (word count: 150)
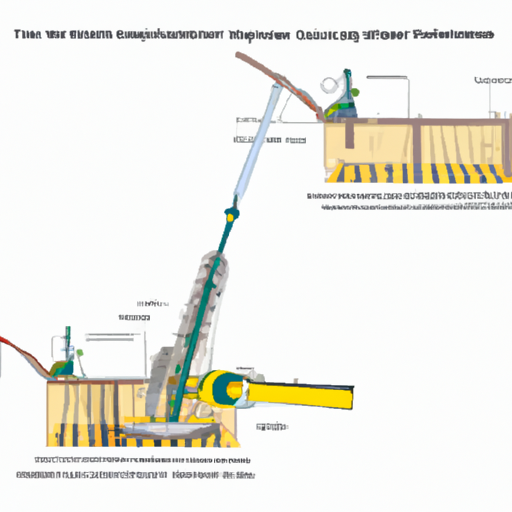
Desilters are hydrocyclone-based devices used in drilling operations to remove solid particles from the drilling fluid, also known as mud. These particles include sand, silt, clay, and other fine solids that can hinder drilling progress and negatively impact equipment performance. Desilters operate on the principle of centrifugal force, where the mud is forced into a rapidly rotating cone-shaped device, separating the solids from the fluid.
2. The Role of Desilters in Drilling Rigs (word count: 200)
Desilters serve as an integral part of the solids control system within drilling rigs. By efficiently removing fine solids from the drilling fluid, desilters help maintain its properties, ensuring optimal drilling performance. Some key functions of desilters include:
a) Enhanced Drilling Fluid Quality: Desilters prevent the accumulation of solids in the drilling fluid, which can degrade its properties. By removing these solids, desilters help maintain the fluid's viscosity, density, and lubricating capabilities, ensuring smooth drilling operations.
b) Equipment Protection: Solid particles present in the drilling fluid can cause abrasion, clogging, and damage to drilling equipment such as mud pumps, bits, and downhole tools. Desilters play a crucial role in protecting these expensive equipment components by removing harmful particles before they reach and potentially harm the equipment.
c) Wellbore Stability: Drilling operations require a stable wellbore to ensure safe and efficient extraction. Solids present in the drilling fluid can destabilize the wellbore by causing formation damage, sloughing, and differential sticking. Desilters help prevent these issues by efficiently removing solids, thereby maintaining wellbore stability.
3. Desilter Components and Operation (word count: 200)
A typical desilter unit consists of several components, including the hydrocyclones, a feed manifold, a discharge manifold, and a motor. The hydrocyclones are the main components responsible for the separation process. They are arranged in a cluster, often referred to as a desilter cone, and are designed to handle a specific flow rate and particle size range.
During operation, the drilling fluid is directed into the desilter through the feed manifold, where it enters the hydrocyclones. The centrifugal force generated by the rotating cone causes the heavier solids to move towards the outer wall and settle at the bottom, while the cleaner fluid rises through the center and exits the hydrocyclone through the discharge manifold. This separation process is continuous, ensuring efficient solids removal from the drilling fluid.
4. Selecting the Right Desilter (word count: 150)
Choosing the appropriate desilter for a drilling rig requires consideration of various factors. These include the drilling rig's specifications, the expected drilling conditions, the desired flow rate, and the anticipated particle size distribution in the drilling fluid. Desilters are available in different sizes and configurations, allowing operators to match the equipment to their specific requirements.
Additionally, it is crucial to regularly monitor and maintain desilters to ensure their optimal performance. This includes inspecting the hydrocyclones for wear and tear, cleaning or replacing damaged parts, and adjusting the operating parameters as necessary.
5. Benefits of Effective Desilter Usage (word count: 200)
Utilizing desilters effectively in drilling operations offers several benefits, including:
a) Increased Drilling Efficiency: By maintaining drilling fluid cleanliness, desilters allow for better drilling penetration rates, reducing overall drilling time and associated costs.
b) Improved Well Productivity: Clean drilling fluid helps minimize formation damage, ensuring better reservoir connectivity and increased well productivity.
c) Enhanced Safety: Efficient desilters contribute to a safer working environment by reducing the risks associated with equipment failures, wellbore instability, and drilling fluid-related accidents.
d) Environmental Considerations: Proper desilter usage reduces the discharge of contaminated drilling fluid into the environment, minimizing the ecological impact of drilling operations.
Conclusion (word count: 100)
Desilters are crucial components in drilling rigs, ensuring the cleanliness and performance of the drilling fluid. By effectively removing solid particles from the fluid, desilters help maintain drilling efficiency, protect equipment, ensure wellbore stability, and improve overall safety. Choosing the right desilter and implementing regular maintenance practices are essential for maximizing their benefits. With their significant impact on drilling operations, desilters play a vital role in the success of drilling projects worldwide.