Enhancing Drilling Rig Efficiency with Desilters: A Comprehensive Guide
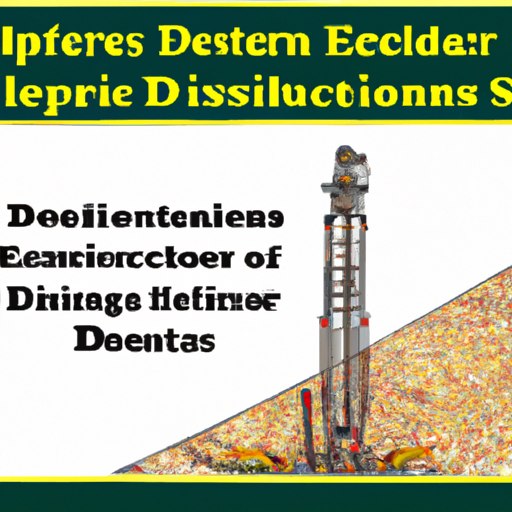
Introduction (150 words)
In the realm of drilling operations, the efficiency and productivity of drilling rigs play a pivotal role. To ensure optimal performance, various equipment and technologies are employed, one of which is the desilter. This article aims to explore the significance of desilters in drilling rigs and their impact on overall operational efficacy. We will delve into the workings of desilters, their benefits, and how they contribute to the success of drilling projects.
1. Understanding Desilters (200 words)
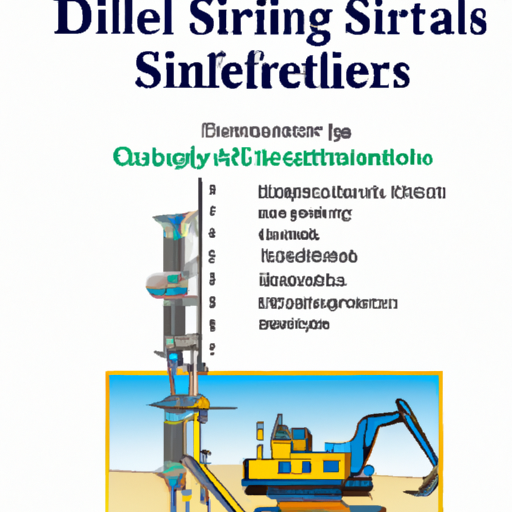
Desilters are integral components of drilling rigs that aid in the separation of solid particles from drilling fluids or mud. They are specifically designed to remove fine particles, typically ranging from 15 to 44 microns in size, from the drilling mud. By efficiently removing these solids, desilters help maintain the optimal performance and longevity of drilling equipment.
2. Operational Mechanism of Desilters (200 words)
Desilters operate on the principle of centrifugal force to separate solid particles from drilling fluids. The drilling mud is pumped into the desilter, where it enters a set of hydrocyclones. These hydrocyclones create a high-speed rotational flow, causing the heavier solids to be thrown towards the walls of the cyclone. The clean drilling mud is then discharged from the overflow ports, while the separated solids are collected from the underflow ports.
3. Key Benefits of Desilters (250 words)
3.1 Enhanced Drilling Fluid Properties:
Desilters play a crucial role in maintaining drilling fluid properties, such as viscosity and density. By removing fine particles, they prevent the mud from becoming excessively thick or heavy, ensuring smooth drilling operations.
3.2 Extended Equipment Lifespan:
The presence of solids in drilling fluids can cause excessive wear and tear on drilling equipment, leading to frequent breakdowns and reduced lifespan. Desilters help mitigate this by efficiently separating solids, reducing equipment maintenance and replacement costs.
3.3 Improved Drilling Efficiency:
By removing fine particles, desilters optimize drilling fluid performance, facilitating efficient drilling processes. This leads to increased drilling speeds, reduced downtime, and overall improved project timelines.
3.4 Environmental Responsibility:
Desilters aid in maintaining a clean and sustainable drilling environment. By effectively removing solids, they contribute to reducing the environmental impact of drilling operations, such as minimizing soil erosion and protecting aquatic ecosystems.
4. Desilter Selection and Maintenance (200 words)
Choosing the right desilter for a drilling rig involves considering factors such as flow rate, operating pressure, and the desired separation efficiency. Regular maintenance is crucial to ensure optimal performance. This includes routine inspections, cleaning of hydrocyclones, and replacement of worn-out components. Adhering to manufacturer guidelines and industry best practices is essential for prolonged desilter efficiency.
5. Conclusion (100 words)
Desilters hold immense significance in drilling rig operations, offering numerous benefits from improved drilling fluid properties to enhanced equipment lifespan and environmental responsibility. By effectively removing fine solids from drilling fluids, desilters optimize drilling operations, leading to increased efficiency and reduced costs. Selecting the appropriate desilter and implementing regular maintenance practices are crucial for obtaining optimum results. Incorporating desilters in drilling rig setups is a wise investment that contributes to the overall success of drilling projects.