The Importance of Desilters in Drilling Rigs: Enhancing Efficiency and Performance
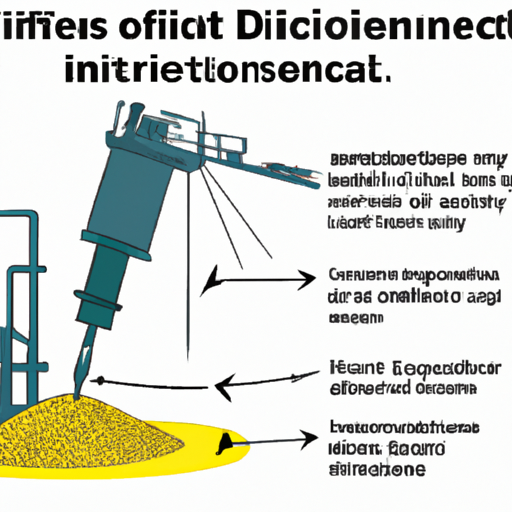
Introduction (150 words)
Drilling rigs play a critical role in the exploration and extraction of oil and gas reserves, and their efficiency and performance are paramount to the success of any drilling operation. In this article, we will delve into the significance of desilters in drilling rigs. Desilters are essential components that aid in the removal of unwanted solids and particles from drilling fluids, ensuring optimal drilling performance and safeguarding the integrity of drilling equipment. With a focus on understanding the functionality, benefits, and key considerations for desilters, this article aims to shed light on their crucial role in drilling operations.
1. Understanding Desilters (200 words)
Desilters are specialized equipment used in drilling rigs to separate and remove fine solids and particles from drilling fluids. They are typically installed downstream from shale shakers and hydrocyclones, and their primary function is to enhance the quality and efficiency of drilling mud. Desilters achieve this by utilizing hydrocyclones, which leverage centrifugal force to separate solid particles from the drilling fluid.
2. The Functionality of Desilters (250 words)
Desilters primarily function by removing particles with a size range of 15 to 47 microns from the drilling fluid. As drilling progresses, the mud containing cuttings and debris is continuously circulated through the desilter unit. The hydrocyclones within the desilter spin the drilling fluid at high speeds, creating centrifugal forces that separate the solid particles from the liquid. The solids are then discharged through an underflow port, while the clean drilling fluid exits through an overflow port, ready to be recirculated.
3. Benefits of Desilters in Drilling Operations (300 words)
a) Enhanced Drilling Fluid Quality: Desilters effectively remove fine solids that can negatively impact drilling fluid properties. By maintaining a high-quality drilling fluid, the desilter contributes to improved drilling penetration rates, reduced wear and tear on drilling equipment, and increased overall drilling efficiency.
b) Extended Equipment Life: The presence of solid particles in drilling mud can cause damage to drilling equipment, such as pumps, mud motors, and drill bits. Desilters prevent these particles from reaching the equipment, thereby prolonging their lifespan and reducing maintenance costs.
c) Reduced Non-Productive Time: Non-productive time (NPT) is a significant concern in drilling operations, as it leads to increased costs and delays. Effective solid removal using desilters helps minimize NPT by preventing equipment failures, maintaining stable drilling conditions, and reducing the need for frequent mud system maintenance.
d) Environmental Stewardship: Desilters play a crucial role in environmental stewardship by removing solid particles from drilling fluids. This ensures that discharged fluids comply with environmental regulations, preventing pollution and minimizing the impact on surrounding ecosystems.
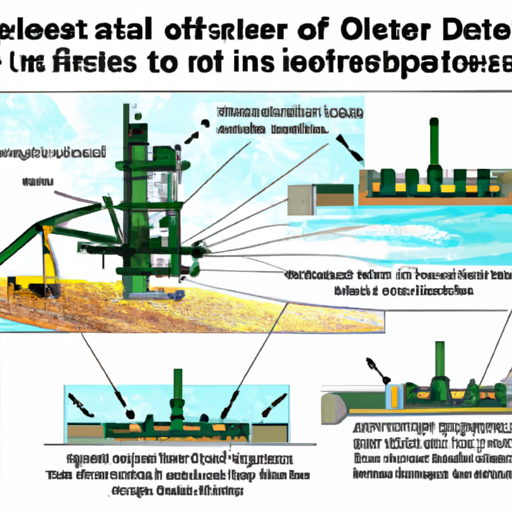
4. Key Considerations for Desilter Selection (200 words)
a) Capacity and Efficiency: The capacity and efficiency of desilters are crucial factors when selecting the appropriate unit for a drilling rig. Manufacturers provide specifications regarding the maximum flow rate and separation efficiency of their desilters. It is important to match these specifications with the drilling rig's requirements.
b) Operating Pressure: Desilters operate under specific pressure conditions, and it is essential to ensure that the selected unit can withstand the pressure exerted by the drilling system.
c) Maintenance and Serviceability: Regular maintenance is necessary to ensure the desilter operates optimally. Consider factors such as ease of maintenance, availability of spare parts, and after-sales support when selecting a desilter for a drilling rig.
Conclusion (100 words)
Desilters are indispensable components of drilling rigs, contributing significantly to the overall efficiency, performance, and environmental sustainability of drilling operations. By effectively removing fine solids from drilling fluids, desilters enhance drilling fluid quality, extend equipment life, reduce non-productive time, and promote environmental stewardship. Selecting the right desilter, considering factors such as capacity, efficiency, operating pressure, and ease of maintenance, is crucial for maximizing the benefits they offer. With the utilization of desilters, drilling rigs can achieve improved drilling performance, reduced costs, and enhanced environmental compliance.