The Ultimate Guide to Plan 62 Mechanical Seal: Enhancing Efficiency and Reliability
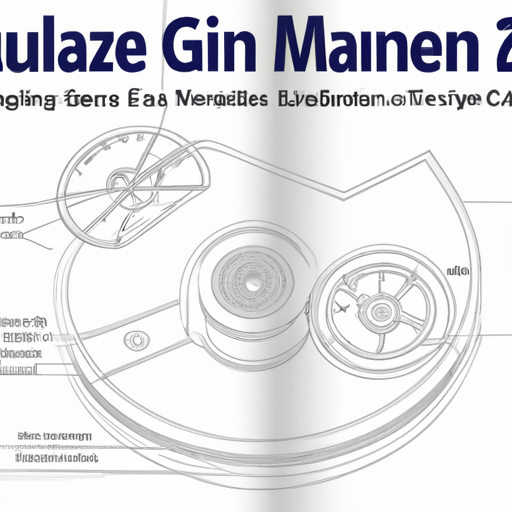
Introduction
Mechanical seals play a crucial role in preventing leakage and ensuring the smooth operation of rotating equipment, such as pumps and compressors. Among the various types of mechanical seals available, the Plan 62 mechanical seal has gained significant popularity due to its exceptional performance in demanding industrial applications. In this comprehensive guide, we will delve into the intricacies of the Plan 62 mechanical seal, exploring its features, benefits, and important considerations.
1. Understanding the Plan 62 Mechanical Seal
The Plan 62 mechanical seal is a robust sealing solution designed to withstand high pressures and temperatures commonly encountered in industrial environments. It incorporates advanced engineering principles to deliver superior performance and reliability. This type of mechanical seal is specifically designed for applications where the pumped fluid is hazardous, toxic, or environmentally sensitive.
2. Key Features and Components
The Plan 62 mechanical seal comprises several key components that work together to ensure effective sealing. These components include:
a. Seal Faces: The seal faces are the primary sealing elements of the Plan 62 mechanical seal. They are typically made from materials such as carbon, ceramic, or silicon carbide, depending on the specific application requirements.
b. Secondary Seals: These seals, including O-rings or elastomers, provide an additional layer of protection against leakage. They are crucial in maintaining a reliable seal even in extreme operating conditions.
c. Gaskets: Gaskets are used to provide a secure and leak-free connection between various components of the mechanical seal. They are commonly made from materials such as rubber, PTFE, or metal.
d. Springs and Bellows: These components provide the necessary force and flexibility to maintain the contact between the seal faces, ensuring a tight seal.
3. Advantages of Plan 62 Mechanical Seals
a. Enhanced Reliability: Plan 62 mechanical seals are specifically designed to offer exceptional reliability, even in demanding applications. Their robust construction and high-quality materials ensure excellent performance and longevity.
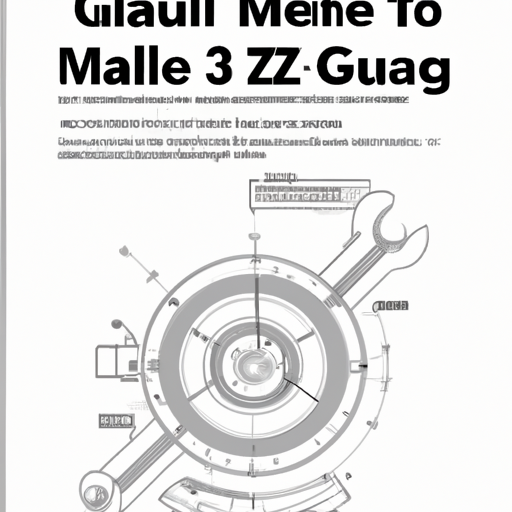
b. Effective Leakage Control: The Plan 62 mechanical seal effectively prevents leakage, minimizing the risk of environmental contamination and ensuring workplace safety.
c. Wide Temperature and Pressure Range: Plan 62 mechanical seals are capable of operating in a wide range of temperatures and pressures, making them suitable for diverse industrial applications.
d. Compatibility with Hazardous Fluids: The Plan 62 mechanical seal's design allows it to handle hazardous and toxic fluids without compromising safety or performance.
e. Reduced Downtime and Maintenance Costs: By providing reliable sealing, Plan 62 mechanical seals help minimize downtime and maintenance requirements, resulting in cost savings for industrial operations.
4. Factors to Consider when Choosing Plan 62 Mechanical Seals
a. Operating Conditions: Understanding the specific operating conditions, including temperature, pressure, and fluid compatibility, is critical in selecting the most suitable Plan 62 mechanical seal for your application.
b. Materials Selection: Different applications may require specific seal face materials to ensure optimal performance and longevity. Consider factors such as chemical compatibility, wear resistance, and thermal conductivity when selecting the appropriate materials.
c. Seal Configuration: Plan 62 mechanical seals are available in various configurations, including single and double seals. Assess your application requirements and consult with experts to determine the most suitable configuration for your needs.
d. Installation and Maintenance: Proper installation and regular maintenance are crucial for maximizing the performance and lifespan of Plan 62 mechanical seals. Ensure that you have access to reliable technical support and follow recommended maintenance practices.
5. Industry Applications
The versatility and reliability of Plan 62 mechanical seals make them suitable for a wide range of industries, including:
a. Oil and Gas: Plan 62 mechanical seals are widely used in upstream, midstream, and downstream operations, including offshore platforms, refineries, and petrochemical plants.
b. Chemical Processing: The chemical industry often deals with hazardous and corrosive fluids, making Plan 62 mechanical seals an ideal choice for pumps and other equipment.
c. Power Generation: Whether it is nuclear, thermal, or hydroelectric power plants, Plan 62 mechanical seals are essential for maintaining efficient and reliable operations.
d. Pharmaceutical and Food Processing: The stringent hygiene and safety requirements in these industries make Plan 62 mechanical seals the preferred choice for maintaining product integrity and preventing contamination.
Conclusion
In conclusion, the Plan 62 mechanical seal is a highly reliable and efficient sealing solution for demanding industrial applications. Its ability to withstand extreme operating conditions, compatibility with hazardous fluids, and enhanced reliability make it a preferred choice across various industries. By considering the factors discussed in this guide, you can select the most suitable Plan 62 mechanical seal for your specific application, ensuring optimal performance, and minimizing downtime and maintenance costs.