Understanding Shale Shaker Screens: A Comprehensive Guide to FLC2000 and FLC503
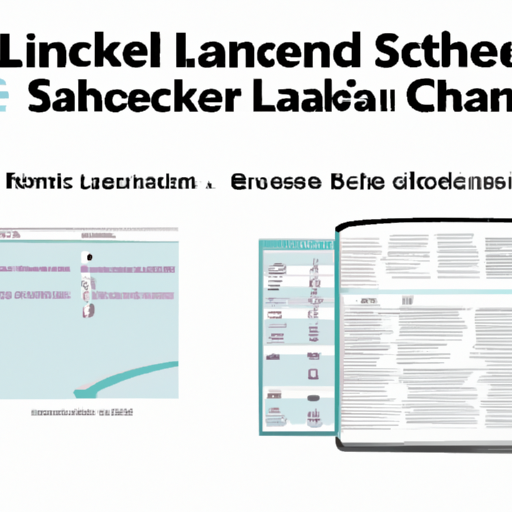
Introduction (100 words)
Shale shaker screens play a critical role in the oil and gas industry's drilling operations. Effective separation of drilling fluids and solids is crucial for the overall drilling process, and the quality and performance of shale shaker screens are key factors in achieving this. In this article, we will delve into the intricacies of shale shaker screens, with a specific focus on the FLC2000 and FLC503 models. We will explore their features, benefits, and how they contribute to efficient solids control in drilling operations.
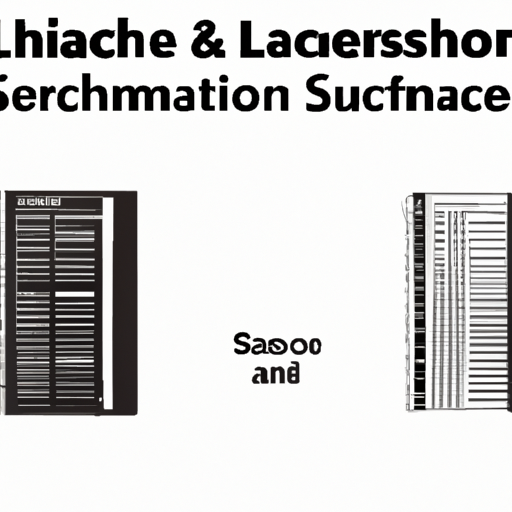
1. Shale Shaker Screens: An Overview (200 words)
Shale shaker screens are crucial components of shale shakers, which are used to separate solids from drilling fluids during the drilling process. These screens act as a sieve, allowing the drilling fluids to pass through while retaining the larger solids, ensuring that the drilling fluids remain clean and reusable.
FLC2000 and FLC503 shale shaker screens are widely recognized for their high efficiency and durability. They are designed to handle high volumes of solids and withstand harsh drilling conditions. Let's take a closer look at their features and advantages.
2. FLC2000 Shale Shaker Screens: Features and Benefits (200 words)
The FLC2000 shale shaker screens are renowned for their superior performance and longevity. They offer several key features that make them ideal for demanding drilling operations. These features include:
a. Increased Screen Area: The FLC2000 screens provide a larger screening area, allowing for enhanced solids removal and better fluid handling capacity.
b. Durability: These screens are constructed with high-quality composite materials, ensuring excellent resistance to wear and tear, even in abrasive drilling environments.
c. Easy Installation: FLC2000 screens are designed for hassle-free installation and removal, enabling quick screen changes and reduced downtime.
d. Versatility: These screens are compatible with various shale shakers, making them a flexible choice for operators using different equipment.
The benefits of FLC2000 shale shaker screens include improved drilling fluid quality, increased drilling efficiency, and reduced operational costs. Their exceptional solids control capabilities contribute to enhanced drilling performance and overall project success.
3. FLC503 Shale Shaker Screens: Features and Benefits (200 words)
Similar to the FLC2000, the FLC503 shale shaker screens are highly regarded for their robustness and performance. These screens offer unique features that ensure optimal solids separation and efficient drilling fluid management. Key features of FLC503 screens include:
a. Pyramid Screen Design: The FLC503 screens boast a pyramid-shaped structure, which enhances the screening efficiency and increases the screen's usable area. This design allows for improved particle separation and better fluid handling capacity.
b. Longevity: The FLC503 screens are manufactured with high-quality stainless steel wire cloth, ensuring exceptional durability and resistance to corrosion and wear.
c. Quick and Easy Screen Changes: These screens utilize a pin-and-hole system, enabling effortless installation and removal. This feature saves valuable time during screen replacement and reduces operational downtime.
d. Compatibility: The FLC503 screens are designed to fit various shale shakers, providing operators with versatile options for their drilling operations.
The benefits of FLC503 shale shaker screens include optimized solids control, extended screen life, reduced maintenance costs, and enhanced drilling efficiency. These screens contribute significantly to achieving a cleaner drilling fluid and minimizing environmental impact.
4. Maintenance and Replacement Considerations (150 words)
To maximize the performance and longevity of shale shaker screens, regular maintenance and timely replacements are crucial. Operators should adhere to the manufacturer's guidelines regarding cleaning, inspection, and replacement intervals. Implementing proper cleaning procedures, such as utilizing appropriate cleaning solutions and techniques, can help prolong screen life and maintain optimal performance.
Additionally, operators should monitor the condition of the screens regularly and replace them when signs of wear, tear, or screen damage are observed. Timely replacement ensures efficient solids control and prevents potential issues that may arise from using worn-out screens, such as reduced separation efficiency and increased drilling fluid costs.
Conclusion (150 words)
Shale shaker screens, particularly the FLC2000 and FLC503 models, are essential components in drilling operations for effective solids control and drilling fluid purification. Their superior features and benefits, including increased screen area, durability, ease of installation, and compatibility, make them ideal choices for demanding drilling environments.
By investing in high-quality shale shaker screens and implementing proper maintenance procedures, operators can optimize drilling efficiency, reduce operational costs, and enhance project success. Regular inspection and timely replacement of worn-out screens are vital for achieving optimal solids separation, maintaining drilling fluid quality, and minimizing environmental impact.
In conclusion, the FLC2000 and FLC503 shale shaker screens are excellent options for operators seeking reliable and efficient solids control solutions. These screens, with their advanced features and exceptional performance, contribute significantly to the success of drilling projects in the oil and gas industry.