Understanding the Advancements in Shale Shaker Screens: A Comparative Analysis of FLC2000 and FLC503
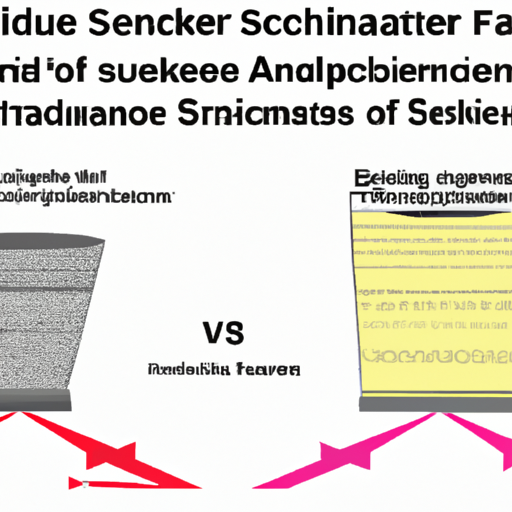
Introduction (100 words):
Shale shaker screens play a vital role in the oil and gas industry, specifically in the drilling process. These screens are responsible for separating solid particles from drilling fluids, ensuring smooth operations and efficient wellbore management. In this article, we will delve into the advancements in shale shaker screens, focusing on two popular models: FLC2000 and FLC503. By understanding their features, benefits, and differences, operators can make informed decisions to optimize their drilling operations and enhance overall productivity.
1. Shale Shaker Screens: A Crucial Component in Drilling Operations (150 words):
Shale shaker screens are designed to remove large solids from drilling fluids, preventing damage to downstream equipment and maintaining the quality of drilling fluids. The FLC2000 and FLC503 shale shaker screens are both widely used in the industry due to their exceptional performance and durability.
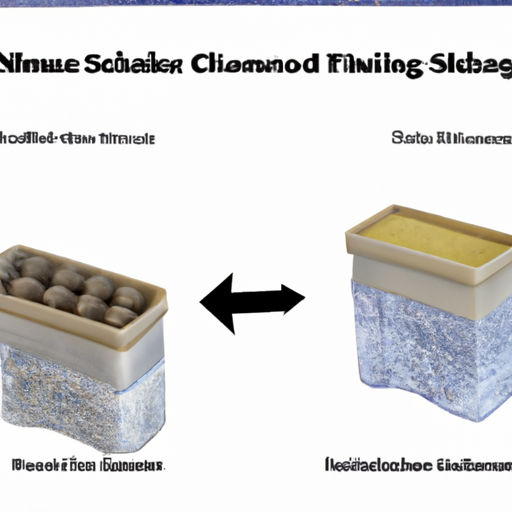
2. Introduction to FLC2000 Shale Shaker Screens (200 words):
The FLC2000 shale shaker screen is a high-quality product that offers remarkable efficiency in solid control applications. It is specifically designed to fit the FLC2000 series of shale shakers, which are commonly used in drilling operations.
The FLC2000 shale shaker screen features an advanced composite frame construction, ensuring excellent resistance to corrosion and abrasion. This makes it suitable for prolonged usage in harsh drilling environments. Additionally, it employs cutting-edge mesh technology, which enhances the screen's conductance, thereby improving the overall fluid handling capacity.
The FLC2000 shale shaker screen is known for its easy installation process, reducing downtime during screen replacement. Its innovative design allows for quick and hassle-free maintenance, further enhancing operational efficiency. Moreover, this screen model offers a wide range of mesh sizes, enabling operators to tailor their solid control systems to specific drilling requirements.
3. Exploring the FLC503 Shale Shaker Screens (200 words):
Similar to the FLC2000 model, the FLC503 shale shaker screen is widely recognized for its exceptional performance and reliability. Designed to fit the FLC503 series shale shakers, this screen model is highly sought after in the oil and gas industry.
The FLC503 shale shaker screen boasts an advanced composite frame construction, ensuring resistance to corrosion, wear, and tear. This makes it suitable for prolonged usage in demanding drilling operations. Furthermore, it incorporates state-of-the-art mesh technology, optimizing fluid handling capacity and ensuring efficient solid control.
The FLC503 shale shaker screen offers effortless installation and maintenance processes. Its user-friendly design allows for quick screen replacement, reducing downtime and enhancing overall operational productivity. Moreover, it provides a wide range of mesh sizes, allowing operators to customize their solid control systems according to their specific drilling needs.
4. A Comparative Analysis: FLC2000 vs. FLC503 Shale Shaker Screens (250 words):
While both the FLC2000 and FLC503 shale shaker screens offer outstanding performance, there are key differences that operators should consider before making a selection.
a) Mesh Technology: The FLC2000 utilizes an advanced mesh technology that enhances fluid conductance, improving overall efficiency. On the other hand, the FLC503 features state-of-the-art mesh technology, optimizing fluid handling capacity and ensuring efficient solid control.
b) Frame Construction: The FLC2000 and FLC503 screens are both constructed with advanced composite frames. These frames provide excellent resistance to corrosion, wear, and tear, ensuring durability and longevity in demanding drilling environments.
c) Compatibility: The FLC2000 shale shaker screen is designed to fit the FLC2000 series shakers, while the FLC503 screen is specifically designed for the FLC503 series shakers. Operators should consider their existing equipment and choose the screen that is compatible with their shaker model.
d) Maintenance and Installation: Both screen models boast user-friendly designs, allowing for easy installation and maintenance. However, operators should consider their specific requirements and select the screen that offers the most seamless replacement process to minimize downtime.
Conclusion (100 words):
Shale shaker screens are essential components in the drilling process, ensuring efficient solid control and maintaining the quality of drilling fluids. The FLC2000 and FLC503 shale shaker screens are two popular models that offer exceptional performance and durability. By understanding their features, benefits, and differences, operators can make informed decisions to optimize their drilling operations. Whether choosing the FLC2000 or FLC503, operators can rest assured that they are investing in high-quality shale shaker screens that will enhance overall productivity and contribute to successful drilling operations.