Shale Shaker Screen: An In-Depth Look at FLC2000 and FLC503 Models
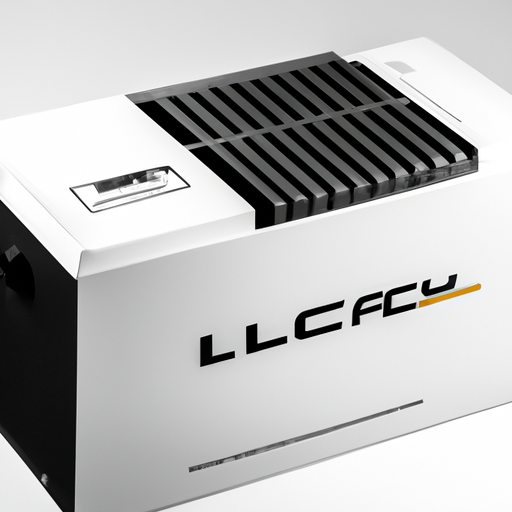
Introduction:
Shale shaker screens are critical components in the drilling industry, used to filter and separate drilling fluids from solids. These screens play a vital role in maintaining the efficiency of the drilling process by ensuring proper solids control. In this article, we will take an in-depth look at two popular shale shaker screen models: FLC2000 and FLC503. We will explore their features, benefits, and applications, providing valuable insights for professionals in the oil and gas industry.
1. Understanding Shale Shaker Screens:
Shale shaker screens are meshed panels that fit on shale shakers, which are large vibrating machines used to separate solids from drilling fluids. These screens act as a barrier, allowing only the fluids to pass through while retaining the solids. The quality of a shale shaker screen directly affects the efficiency of the drilling operation, making it crucial to select the right screen for the job.
2. FLC2000 Shale Shaker Screen:
The FLC2000 shale shaker screen is a widely used model known for its excellent performance and durability. It is designed to fit the FLC2000 series of shale shakers, which are commonly used in oil and gas drilling operations. Let's explore some key features and benefits of this screen:
2.1. Mesh Design and Material:
The FLC2000 shale shaker screen is constructed using high-quality stainless steel wire mesh. The mesh size can vary depending on the application but is typically between 20 and 325 mesh. The mesh design ensures efficient solids control while allowing the drilling fluids to pass through seamlessly.
2.2. Frame Structure:
The FLC2000 shale shaker screen features a rugged frame structure, typically made of carbon steel or composite material. This frame provides stability and support to the screen, ensuring its longevity even under harsh drilling conditions.
2.3. Quick and Easy Installation:
The FLC2000 shale shaker screen is designed for easy installation and replacement. It features a hook strip or pretensioned design, allowing for quick screen changes without the need for additional tools. This efficient installation process minimizes downtime and maximizes productivity on drilling sites.
2.4. Improved Solids Control Efficiency:
The FLC2000 shale shaker screen offers exceptional solids control efficiency. Its precise mesh design effectively separates solids from drilling fluids, preventing clogging and maximizing the fluid's clarity. This translates to improved drilling performance and reduced operational costs.
2.5. Versatile Applications:
The FLC2000 shale shaker screen is suitable for a wide range of drilling applications, including oil and gas exploration, geothermal drilling, water well drilling, and HDD (Horizontal Directional Drilling). Its versatility makes it a popular choice for drilling contractors and operators worldwide.
3. FLC503 Shale Shaker Screen:
The FLC503 shale shaker screen is another well-regarded model used in the drilling industry. It is specifically designed to fit FLC503 shale shakers, which are commonly used in offshore drilling applications. Let's delve into the features and benefits of this screen:
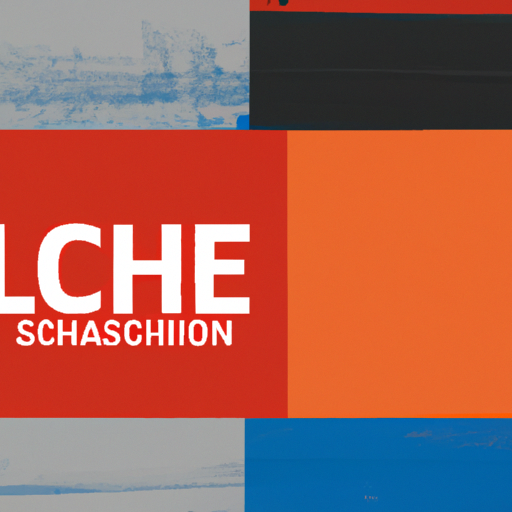
3.1. High-Quality Construction:
The FLC503 shale shaker screen is constructed using high-grade stainless steel wire mesh. The mesh size can be customized based on the drilling requirements, ensuring optimal solids control efficiency. The screen's robust construction guarantees durability even in demanding offshore drilling environments.
3.2. Corrosion Resistance:
Offshore drilling operations often involve exposure to harsh marine environments, including saltwater and corrosive elements. The FLC503 shale shaker screen is corrosion-resistant, thanks to its stainless steel construction. This corrosion resistance extends the screen's lifespan and reduces the need for frequent replacements.
3.3. Enhanced Performance:
The FLC503 shale shaker screen is designed to deliver excellent performance in offshore drilling applications. Its precise mesh design efficiently separates solids from drilling fluids, maintaining the fluid's viscosity and preventing loss of valuable drilling materials. This screen's performance ensures reliable solids control, even in challenging offshore conditions.
3.4. Easy Maintenance and Replacement:
Maintaining and replacing shale shaker screens is crucial to prevent operational disruptions. The FLC503 shale shaker screen offers easy maintenance and replacement, thanks to its user-friendly design. The hook strip or pretensioned installation options enable quick and hassle-free screen changes, minimizing downtime and optimizing drilling operations.
3.5. Reliable Offshore Applications:
The FLC503 shale shaker screen is specifically designed for offshore drilling applications, where efficiency and reliability are paramount. Its high-performance capabilities make it an ideal choice for offshore drilling contractors, ensuring uninterrupted operations and improved overall productivity.
4. Conclusion:
Shale shaker screens, such as the FLC2000 and FLC503 models, are indispensable components in the drilling industry. Their efficient solids control capabilities and durable construction make them essential for maintaining drilling fluid quality and maximizing operational efficiency. Whether it's onshore or offshore drilling, selecting the right shale shaker screen is crucial for optimal drilling performance.
The FLC2000 and FLC503 shale shaker screens are renowned for their exceptional features, including precise mesh design, durable frame structure, easy installation, and reliable solids control efficiency. Understanding their unique benefits and applications empowers drilling professionals to make informed decisions when choosing the appropriate shale shaker screen for their specific drilling needs.