Desilter in Drilling Rig: Enhancing Efficiency and Optimizing Solids Control
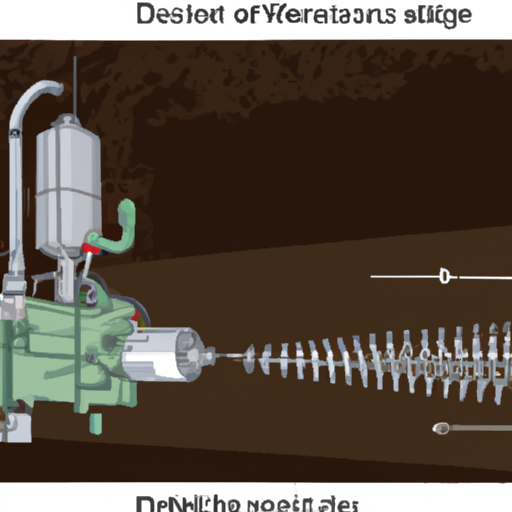
Introduction
In the realm of drilling operations, the efficient management of drilling fluids and the removal of solid particles are crucial for maintaining wellbore stability, optimizing drilling performance, and ensuring the safety of personnel and equipment. To achieve this, modern drilling rigs are equipped with various solids control equipment, including desilters. In this article, we will delve into the role of desilters in drilling rigs, highlighting their importance, functionality, and benefits in enhancing drilling efficiency.
Understanding Solids Control in Drilling Operations
Drilling fluids, commonly known as mud, play a pivotal role in drilling operations. They serve multiple purposes, including lubrication, cooling, and carrying cuttings to the surface. However, during the drilling process, the mud tends to accumulate solid particles such as drill cuttings, shale, and sand. If left unchecked, these solids can adversely impact drilling performance, leading to equipment failures, reduced drilling rates, and wellbore stability issues.
Therefore, effective solids control is imperative to maintain the desired drilling fluid properties and remove unwanted solids. Solids control equipment, including shale shakers, hydrocyclones, and desilters, are employed in drilling rigs to achieve this objective.
Understanding Desilters
Desilters are a vital component of the solids control system that focuses on the removal of fine solids (typically ranging from 15 to 44 microns) from the drilling fluid. They are hydrocyclone-based devices designed to separate the finer particles from the drilling mud, allowing for the reuse of the fluid while disposing of the solids.
Functionality of Desilters
Desilters operate on the principle of centrifugal force and hydrocyclonic separation. The drilling fluid containing the solid particles enters the desilter unit through an inlet manifold. It then passes through a series of hydrocyclones, which are cone-shaped devices with an apex at the bottom.
The high-speed rotation of the drilling fluid within the hydrocyclone generates centrifugal force, causing the heavier particles to move towards the wall of the cone. As the fluid spirals downward, the finer particles are forced towards the center of the cone, forming an upward spiral flow. This flow exits the hydrocyclone through the overflow outlet, while the separated solids are discharged through the underflow outlet.
Advantages of Desilters in Drilling Operations
1. Improved Drilling Fluid Quality: By removing fine solids, desilters enhance the quality and properties of the drilling fluid, ensuring its optimal performance in various drilling activities. This leads to improved hole stability, reduced torque and drag, and enhanced drilling penetration rates.
2. Cost Savings: Efficient desilter usage results in cost savings by reducing the consumption of drilling fluids. Reusing the treated drilling mud minimizes fluid expenses and waste disposal costs, contributing to overall project profitability.
3. Enhanced Equipment Performance: Desilters prevent the accumulation of solids in downstream equipment, such as centrifuges and mud cleaners, thereby extending their lifespan. Minimizing the presence of solids also reduces pump wear and tear, improving overall equipment efficiency and reducing maintenance costs.
4. Environmental Benefits: Proper solids control, facilitated by desilters, ensures that drilling fluids are properly treated before being discharged into the environment. This minimizes the environmental impact of drilling operations by reducing the release of contaminants into water bodies or soil.
5. Operator Safety: By effectively removing solid particles, desilters contribute to a safer working environment by reducing the risks associated with drilling fluid contamination, such as chemical exposure and equipment malfunctions.
Optimizing Desilter Performance
To maximize the benefits of desilters, several key considerations should be addressed:
1. Proper Sizing: Selecting the appropriate desilter size based on the drilling rig's specifications and anticipated drilling conditions is crucial for optimal performance. Factors such as flow rate, pressure, and desired particle size separation should be considered during the selection process.
2. Maintenance and Monitoring: Regular inspection and maintenance of desilters are essential to ensure their consistent performance. This includes cleaning the hydrocyclones, checking for wear or damage, and replacing worn parts when necessary. Additionally, monitoring the pressure differentials across the desilters helps identify any potential issues and allows for timely adjustments.
3. Integration with Solids Control System: Desilters should be seamlessly integrated into the overall solids control system of the drilling rig. Proper positioning and alignment with other equipment, such as shale shakers and mud cleaners, ensure efficient flow and effective solids control throughout the drilling operation.
Conclusion
Desilters play a critical role in maintaining drilling fluid quality, optimizing solids control, and enhancing drilling efficiency in modern drilling rigs. By effectively removing fine solids from the drilling mud, desilters improve wellbore stability, reduce equipment wear, and minimize environmental impact. Incorporating desilters into drilling operations not only enhances drilling performance but also contributes to cost savings and operator safety. Therefore, their proper selection, integration, and regular maintenance are essential for maximizing their benefits and ensuring efficient drilling operations.
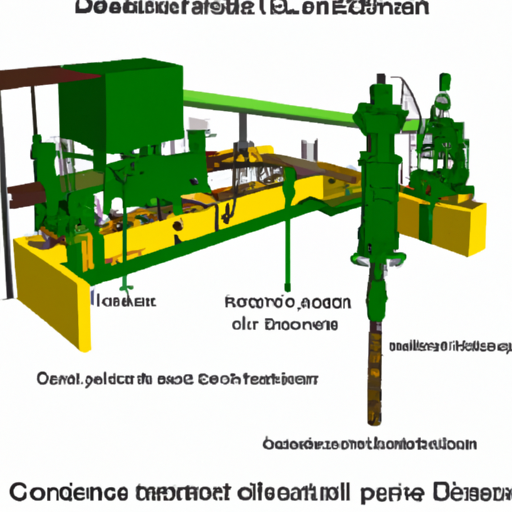