Enhancing Efficiency and Safety: The Evolution of Oil Rig Elevators
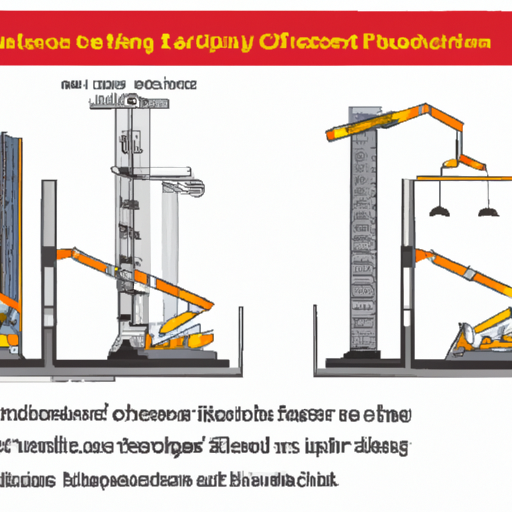
Introduction (100 words):
Oil rig elevators play a pivotal role in enhancing the efficiency and safety of offshore drilling operations. These complex mechanical systems provide essential transportation for personnel, equipment, and supplies between different levels of the rig. Over the years, advancements in technology and engineering have revolutionized the design and functionality of oil rig elevators. In this article, we will explore the evolution of oil rig elevators, highlighting the key features, safety measures, and advancements that have made them vital components of the offshore drilling industry.
1. The Importance of Oil Rig Elevators (150 words):
Oil rig elevators are critical for maintaining smooth operations on offshore drilling platforms. These elevators transfer personnel, materials, and heavy equipment vertically, reducing the need for manual lifting or using cranes. By streamlining transportation, oil rig elevators enhance operational efficiency, saving time and minimizing downtime.
Furthermore, the safety of offshore workers is significantly improved by utilizing elevators. With the ability to transport employees quickly and safely, elevators reduce the risks associated with climbing stairs or ladders, especially in harsh weather conditions. Additionally, the efficient transportation of heavy equipment and supplies reduces the strain on workers, minimizing fatigue-related accidents.
2. Traditional Oil Rig Elevators (200 words):
Early oil rig elevators were simple, cage-like structures operated by manual pulley systems. These elevators were primarily used for vertically transporting personnel and light equipment. They were limited in capacity and slower in operation, often leading to delays and inefficiencies.
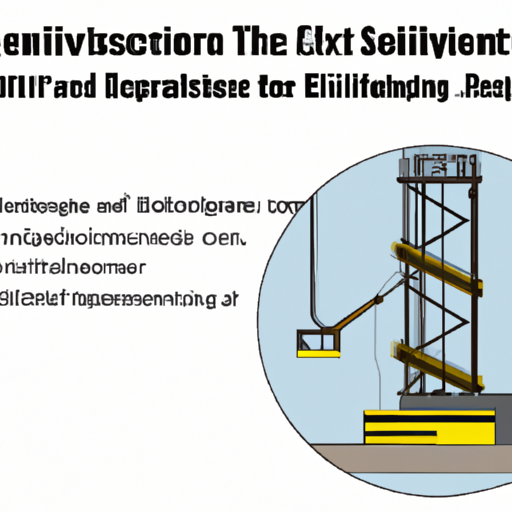
As offshore drilling operations expanded, the demand for more robust and efficient elevators increased. In response, hydraulic-driven elevators were introduced. These elevators utilized hydraulic systems to power the lifting mechanism, allowing for higher capacities and faster transportation. However, they still had limitations, including the risk of hydraulic fluid leaks and the need for regular maintenance.
3. Modern Oil Rig Elevators (300 words):
The evolution of oil rig elevators witnessed a significant breakthrough with the introduction of electric-powered elevators. Electric elevators eliminated the need for hydraulic systems, leading to enhanced safety and reliability. These modern elevators are designed with advanced control systems, allowing for smooth and precise vertical transportation.
One of the key advancements in modern oil rig elevators is their increased capacity. Elevators capable of carrying heavy loads, such as drilling machinery and equipment, have become commonplace. This has greatly reduced the reliance on cranes and manual lifting, streamlining operations and reducing the risk of handling-related accidents.
Safety features have also been incorporated into modern oil rig elevators to protect workers in emergency situations. These features include fire-resistant materials, emergency braking systems, and backup power supplies. In the event of a power failure or emergency, these elevators can safely transport personnel to a secure location.
Furthermore, modern oil rig elevators have implemented advanced control systems, such as programmable logic controllers (PLCs), to monitor and regulate the elevator's performance. These systems can detect abnormalities in operation, enabling preventive maintenance and reducing the risks of malfunctions or breakdowns.
4. Advancements in Maintenance and Inspection (250 words):
To ensure the safe and efficient operation of oil rig elevators, regular maintenance and inspections are crucial. Technological advancements have simplified these processes, minimizing downtime and enhancing safety.
Remote monitoring and diagnostic systems have been incorporated into modern elevators, enabling real-time monitoring of key parameters. This allows maintenance technicians to identify potential issues and perform proactive maintenance remotely, reducing the need for physical inspections and minimizing disruptions to operations.
Additionally, the use of non-destructive testing techniques, such as ultrasonic testing and magnetic particle inspection, has become common practice. These techniques help identify any hidden defects or structural weaknesses in elevator components, ensuring their integrity and safe operation.
Conclusion (100 words):
Oil rig elevators have come a long way, evolving from simple manual systems to sophisticated electric-powered machines. These elevators have revolutionized offshore drilling operations, enhancing efficiency and safety. The increased capacity, advanced safety features, and improved maintenance and inspection techniques have made oil rig elevators an integral part of the industry. As technology continues to advance, we can expect further innovations in oil rig elevator design, further enhancing the efficiency and safety of offshore drilling operations.