Enhancing Drilling Performance and Reliability with 4145H Spiral Drill Collars
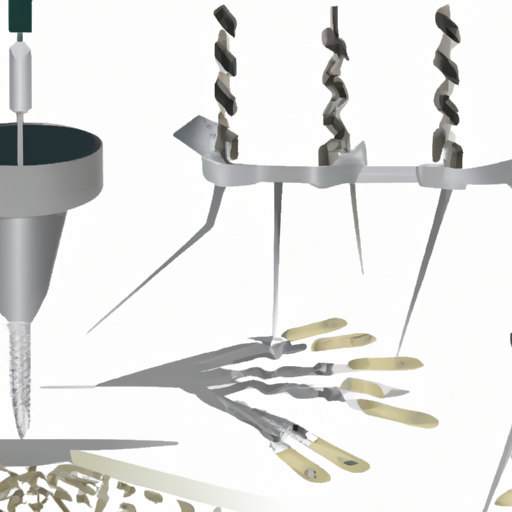
Introduction:
The oil and gas industry heavily relies on drilling operations for exploration and extraction. To ensure efficient and successful drilling, it is crucial to utilize high-quality drilling tools and equipment. Among these tools, drill collars play a significant role in maintaining stability and weight on the drill bit. In recent years, the 4145H spiral drill collar has emerged as a game-changer in the industry, offering superior strength, durability, and performance. This article delves into the benefits and features of 4145H spiral drill collars, exploring how they enhance drilling operations.
1. Understanding Drill Collars:
Drill collars are thick-walled, heavy-duty tubular components placed between the drill pipe and drill bit. Their primary purpose is to provide weight to the drill bit and maintain the verticality of the drill string. Drill collars also help control bending stress and vibration, ultimately improving drilling performance. Various materials are used in their construction, with the 4145H steel alloy being one of the most preferred choices.
2. The Significance of 4145H Steel Alloy:
The 4145H steel alloy is a high-quality, heat-treated steel renowned for its exceptional mechanical properties. It exhibits high tensile and yield strength, making it ideal for demanding drilling conditions. Its unique chemical composition, including elements such as chromium, molybdenum, and manganese, enhances its toughness, corrosion resistance, and wear resistance. These properties make 4145H an excellent choice for manufacturing drill collars designed to withstand extreme drilling forces.
3. The Advantages of Spiral Drill Collars:
Spiral drill collars, including the 4145H variant, offer several advantages over conventional drill collars. One significant advantage is their increased torsional and bending strength, which helps prevent buckling and failure during drilling operations. The spiral design, characterized by continuous grooves wrapped around the collar, enhances contact with the wellbore, reducing sticking and differential sticking issues. Additionally, the spiral grooves provide better circulation of drilling fluids, reducing the risk of drill string vibration and improving hole cleaning.
4. Enhanced Wear Resistance and Fatigue Life:
Drilling operations expose drill collars to harsh environments, including abrasion, corrosion, and fatigue. The 4145H spiral drill collars excel in these challenging conditions. The combination of the 4145H steel alloy's exceptional wear resistance and the spiral design's improved fluid circulation significantly reduces wear and tear. This results in extended drill collar life and reduced downtime for maintenance and replacement.
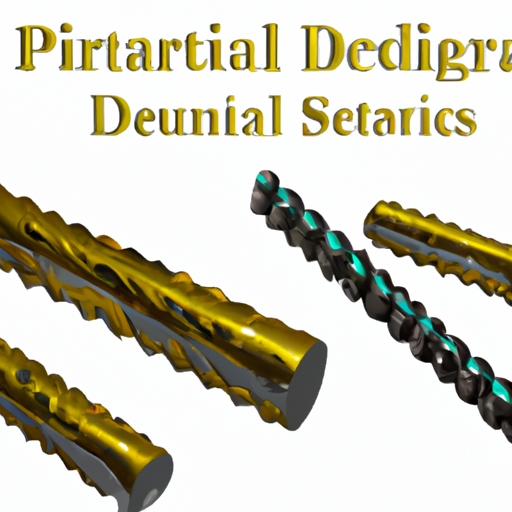
5. Improved Drilling Stability and Control:
Maintaining drilling stability and control is crucial for efficient and safe operations. Spiral drill collars, such as the 4145H variant, enhance stability by reducing drill string vibrations and controlling wellbore deflection. The spiral grooves provide additional contact points between the drill collar and the wellbore, thereby minimizing eccentricity. This improved stability ensures accurate drilling, reduces the risk of costly wellbore deviations, and increases overall drilling efficiency.
6. Compatibility and Versatility:
The 4145H spiral drill collars are designed to be compatible with various drilling systems, making them versatile and easily integrated into existing drilling operations. They can be used in both vertical and directional drilling applications, offering consistent performance across different drilling environments. The versatility of 4145H spiral drill collars makes them a reliable choice for oil and gas companies operating in diverse geological conditions.
7. Industry Standards and Quality Assurance:
To ensure the reliability and performance of drill collars, adherence to industry standards is essential. Leading manufacturers of 4145H spiral drill collars comply with specific quality control measures, including API (American Petroleum Institute) standards. These standards ensure that the drill collars meet strict criteria for material composition, heat treatment, dimensional accuracy, and mechanical properties. By choosing drill collars from reputable manufacturers, companies can guarantee the highest levels of quality and performance.
Conclusion:
The 4145H spiral drill collar has revolutionized the drilling industry by offering enhanced strength, durability, and performance. Its unique properties, including high tensile strength, wear resistance, and improved fluid circulation, make it the preferred choice for demanding drilling operations. The spiral design of these drill collars improves stability, reduces vibration, and enhances overall drilling efficiency.
Investing in high-quality drill collars like the 4145H variant ensures reliable and efficient drilling operations, minimizing downtime, and reducing maintenance costs. As the oil and gas industry continues to evolve, the use of advanced and innovative drilling tools, such as the 4145H spiral drill collar, will play a crucial role in maximizing productivity and achieving success in exploration and extraction endeavors.